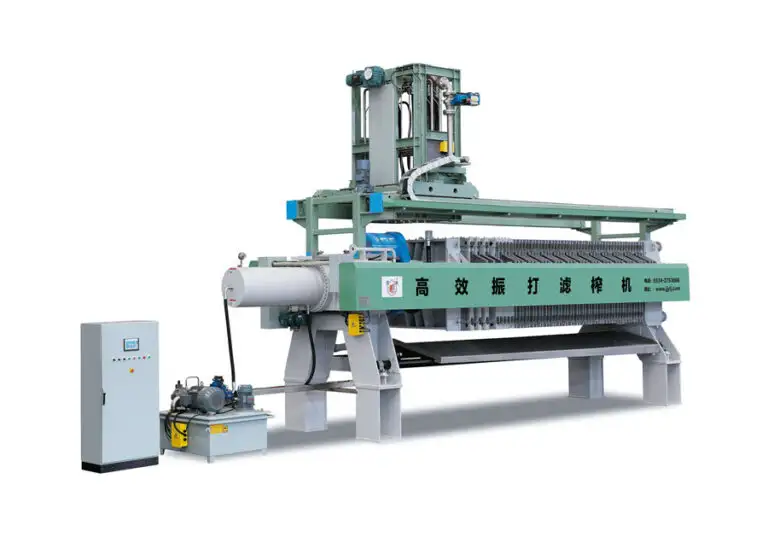
Wholesale China Filter French Press Price
For customized product solutions, please reach out to us!
Your satisfaction is our guarantee!
Jingjin will always be your reliable partner!
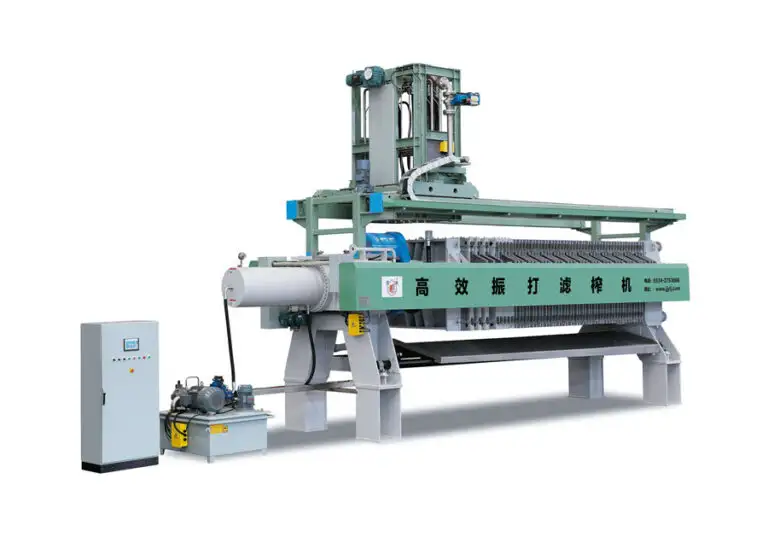
Quick Details
Supply Ability
Supply Ability:10000 Set/Sets per Year
Packaging & Delivery
Packaging Details: Seaworthy packing: Big part: plastic film winding , fix well in the container. Small part: iron box
Port: customer specified
Lead Time: One month
Application areas of Filter French Press
Filter presses are widely used in a variety of fields, including food and beverage processing, chemical production, mining, power generation, aggregate, asphalt and cement production, steel mills and municipal plants. It achieves precise separation of liquids and solids by controlling the filtration process, and is cost-effective, easy to clean and maintain. Filter presses are available in a variety of configurations and can be customized to meet specific application requirements, including the number of filter chambers, filter plate size, construction materials, and other features such as automatic filter plate changer, filter cloth cleaning system, etc.
Wholesale Tube Press Filter China Factory
Established in 1998, Jingjin Environmental Protection Inc. has become a comprehensive leader in environmental protection services. The company specializes in the production of filtration equipment, offers complete filtration technology solutions, and manages environmental protection projects from inception to completion.
Jingjin holds the position of vice-president within the China Environmental Protection Industry Association and has been instrumental in drafting national standards for filter presses and plates. For twelve consecutive years, Jingjin has maintained the largest production capacity and sales volume of filter presses globally, exporting to 123 countries and regions.
The Jingjin trademark has been recognized as a “China Famous Brand” by the State Administration for Industry and Commerce of the People’s Republic of China and is protected under the Madrid International Trademark Registration. Water Jiang, the chairman of Jingjin, has been honored with the titles of National Model Worker and National Labor Model.
Introduction of Advanced German Equipment by JINGJIN
Jingjin is dedicated to advancing energy conservation and environmental protection, providing consumers with cost-effective products and high-quality services. To meet stringent filtration requirements, Jingjin has introduced a complete set of German filter cloth production lines and technology.
With 27 years of expertise in filtration, Jingjin employs robust German rapier looms to weave the finest silk threads into high-density filter cloths with various hole patterns. This process utilizes a beating-up force of 0.3-3.5 tons after each weft crosses the warp. Jingjin’s filter cloths feature 50% more filtration holes per unit area compared to others, significantly enhancing filtration speed. The cloth is woven under controlled temperature and humidity conditions to eliminate fabric burrs caused by static electricity.
A key innovation is the monofilament filter cloth’s ability to facilitate the automatic detachment of filter cakes, effectively resolving a long-standing industry challenge.
JINGJIN: A Leading Global Service Provider
Jingjin is committed to realizing its vision of becoming the world’s leading environmental protection service provider. With a mission to “protect the environment and beautify China,” Jingjin’s eco-friendly strategy focuses on “turning sewage into pure water and sludge into resources.” This approach offers comprehensive solutions for environmental protection and economic development, aiming to leave a cleaner environment with pure water and clear skies for future generations.
Technical Advantages
1.Enhanced Frame Material: The frame of the Jingjin filter press is constructed from Q345B steel, which offers a tensile strength 1.4 times higher than that of Q235. This ensures that the filter press operates with enhanced safety and stability.
2.Precision Welding: The cylinder seat, pressure plate, and thrust plate are crafted using carbon dioxide shielded welding, providing robust and reliable construction.
3.Advanced Beam Design: The main beam features a welded box structure, manufactured using state-of-the-art submerged arc automatic welding technology, which enhances the overall structural integrity.
4.Superior Surface Treatment: All components requiring painting undergo high-speed centrifugal shot blasting to effectively remove rust and scale. Following this, an MIO epoxy build primer is applied, and acrylic urethane paint is directly coated for optimal adhesion. This process saves hundreds of tons of putty annually, reducing costs and environmental impact. Moreover, it significantly enhances the paint’s adhesion and the filter press’s anti-corrosion properties.
If you are interested in our products, please contact us !