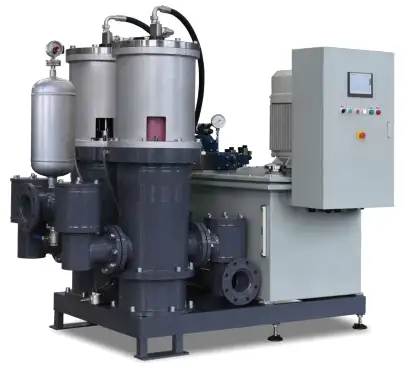
Jingjin High pressure Plunger type Feeding pump
For custom solutions, please don't hesitate to reach out to us!
Your satisfaction is our commitment!
Jingjin will always be your dedicated partner!
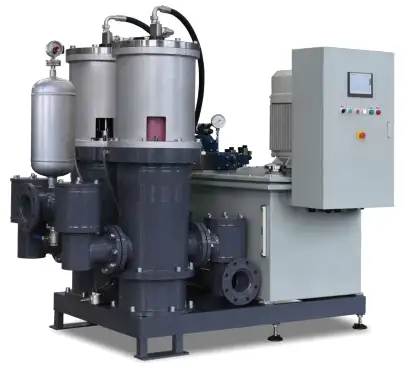
The application areas of High pressure Plunger type Feeding pump are as follows
1.Chemical Processing: High-pressure plunger pumps are utilized for metering and dosing chemicals, transferring corrosive fluids, and for other processes requiring precise control and high pressures.
2.Oil and Gas Industry: These pumps are used in oil well stimulation (such as fracking), injection of fluids into wells, and for various drilling operations.
3.Water Treatment: They are employed in reverse osmosis systems for desalination, water purification, and wastewater treatment, where high pressures are needed to force water through membranes.
4.Power Generation: In power plants, high-pressure plunger pumps are used for boiler feedwater systems, chemical dosing, and other critical applications that require high-pressure fluid delivery.
5.Food and Beverage Industry: For applications like the dosing of additives, flavorings, and other ingredients that require precise measurement and delivery under high pressure.
Jingjin Intelligent Energy-Saving Feed Plunger Pump: Features and Innovative Advantages
1.Wear Resistance: The plunger is crafted from alumina ceramic, achieving a surface roughness of 0.4μm and a hardness exceeding HRC8.5 after precision grinding. This design minimizes shear movement between the plunger and the conveyed material, making it particularly effective for materials containing sand and solid particles.
2.Strong Self-Absorption Capability: Utilizing a plunger vacuuming method, the pump boasts a self-priming capacity of 4-8 meters, with the suction range varying based on the material’s specific gravity.
3.Compact Design: Featuring a built-in plunger cylinder structure, the pump’s height is reduced compared to conventional vertical plunger pumps. The integrated cooling channel ensures no leakage of circulating water, maintaining a clean and tidy site.
4.Energy Efficiency: The pump employs a large-diameter, double-cylinder hydraulic double pump design, automatically adjusting the required pressure based on the filter press’s working conditions to maximize efficiency and energy savings.
5.Intelligent Control: With dynamic pressure acquisition, intelligent flow control, and soft piston reversing, the pump significantly reduces vibration and noise, ensuring smooth operation.
6.Simple Operation: Pressure adjustments are straightforward, requiring only the tightening or loosening of the pressure regulating valve. Once set, the valve is locked, eliminating the need for further adjustments.
7.Aesthetic Design: The pump’s main body undergoes sandblasting and spray painting processes to relieve stress and ensure the adhesion and aesthetics of the anticorrosive paint.
8.Safety and Reliability: Equipped with a safety pressure sensor, temperature overheat protection sensor, and action timeout alarm, the pump ensures safe operation.
9.Top-Brand Electrical Components: The cabinet’s low-voltage appliances are from Schneider, and the PLC is from Siemens, ensuring high-quality performance.
10.Versatile Control Options: The pump offers both remote and local control. Local control is managed via the piston pump’s control cabinet, while remote control can be achieved through hard wiring, MODBUS, or Ethernet, allowing communication with the filter press’s control cabinet or upper computer.
11.High Rated Pressure: The feed pressure ranges from 0-2.0 MPa, with specifications available for 2.0 MPa to 3.5 MPa, and a rated water pressure reaching up to 1.8 MPa.
12.Optimized for Filter Press Feeding Stages:
13.Initial Feeding Stage: The filter press chamber is empty, requiring rapid material filling. Both large and small displacement hydraulic pumps operate simultaneously to achieve maximum flow.
Pressure Filtration Stage: As the filter press fills, pressure rises and water is expelled. The piston pump adjusts to increasing cavity pressure by switching to a large displacement hydraulic pump, meeting high-pressure, large-flow feeding needs.
Pressure Holding Filtration Stage: Upon reaching the highest set pressure, the pump maintains constant pressure filtration by switching to a small displacement hydraulic pump, conserving energy while meeting pressure holding demands.
Low Maintenance Cost: The pump’s vulnerable components, such as the valve plate and plunger seal, have a replacement cycle of six months for ceramic mud and twelve months for municipal sludge.
14.Long Service Life: The pump is designed to last at least 15 years.
15.Customized Production: Products are tailored to each user’s specific working conditions, offering flexible configurations to suit customer production needs.
If you are interested in our products, please contact us !