How Do You Choose The Right Filter Plate For a Specific Application?
Ott 12, 2024
Selecting the appropriate filter plate for your specific application is critical for ensuring optimal performance in a filter press system. This article explores the essential factors to consider when choosing filter plates, from their material composition to their design features. Jingjin is a leading filter plate manufacturer dedicated to providing high-quality filter plates that meet the diverse needs of various industries. Our advanced manufacturing processes utilize state-of-the-art technology and high-grade materials to produce filter plates designed for optimal performance and durability.
What is a filter plate, and what role does it play in a filter press?
A filter plate is a key component of a filter press, serving as a barrier that separates solids from liquids during the filtration process. The filter plates create chambers where the slurry is introduced, allowing the liquid to pass through while retaining solid particles. The efficiency of solid-liquid separation largely depends on the quality and type of filter plates used in the system.
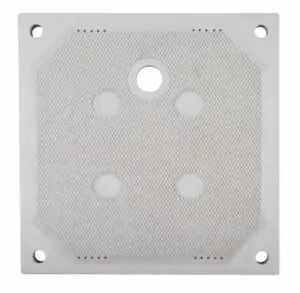
What materials are commonly used to manufacture filter plates?
Filter plates are typically made from various materials, each offering distinct advantages based on the application requirements. Common materials include:
Polypropylene: Lightweight, corrosion-resistant, and suitable for a range of chemical applications.
Stainless steel: Known for its durability and ability to withstand high temperatures and pressures, making it ideal for demanding environments.
Cast iron: Often used in heavy-duty applications due to its strength, although it is more susceptible to corrosion.
Rubber-coated plates: Provide additional protection against wear and tear, especially in abrasive conditions.
How does the design of a filter plate affect its performance?
The design of a filter plate can significantly influence its filtration performance. Key design features include:
Recessed or membrane plates: Recessed plates create deeper chambers for holding more solids, while membrane plates allow for additional pressure application to enhance cake dryness.
Surface texture: A textured surface can improve cake release and enhance drainage, increasing overall efficiency.
Drainage design: Effective drainage patterns facilitate better liquid flow and minimize clogging.
How do filter plates contribute to the efficiency of solid-liquid separation?
Filter plates play a crucial role in solid-liquid separation by optimizing the filtration process. Their design, material, and surface characteristics determine the rate at which solids are captured and liquids are released. Properly chosen and maintained filter plates help reduce cycle times, improve product quality, and lower operational costs.
What is the average lifespan of a filter plate in industrial applications?
The lifespan of a filter plate varies based on factors such as material, application, and maintenance practices. Generally, filter plates can last anywhere from 1 to 10 years, with polypropylene plates typically having a shorter lifespan compared to stainless steel plates. Regular inspections and timely replacements are essential to ensure optimal performance and avoid costly downtime.
How do you maintain and clean filter plates for optimal performance?
Regular maintenance and cleaning are vital for extending the lifespan of filter plates and ensuring optimal performance. Here are some best practices:
*Routine inspections: Check for wear, cracks, and signs of clogging.
*Cleaning protocols: Use appropriate cleaning agents and methods, such as high-pressure water jets, to remove accumulated solids and prevent cross-contamination.
*Proper storage: Store filter plates in a dry, cool place to prevent damage from environmental factors.
What are the common issues encountered with filter plates during operation?
Filter plates can experience various issues that may affect their performance, including:
Clogging: Accumulation of solids can impede liquid flow and reduce efficiency.
Cracking or warping: Caused by excessive pressure or thermal stress, leading to leaks and reduced effectiveness.
Worn surfaces: Regular use can wear down the surface texture, impacting filtration efficiency.
In conclusion, choosing the right filter plate for your specific application requires careful consideration of material, design, size, and maintenance practices. By understanding these factors, you can optimize the performance of your filter press system and achieve efficient solid-liquid separation. As a prominent filter plate supplier, Jingjin is committed to delivering top-notch filtration solutions to our customers worldwide. We pride ourselves on our extensive inventory of filter plates, available in various sizes and materials to cater to different applications. Our knowledgeable team provides exceptional customer service, assisting clients in selecting the right filter plates for their specific needs.